CAD Trainings and coaching
CAD-trainings with a set agenda or individual coaching on your desired topics
CAD trainings in general
Through many years of experience in CAD design and in the strategic development of complex models and extensive assemblies, R‑Kon has an extensive fund of knowledge in the use of CAD systems, especially Autodesk Inventor. For customers who want to expand their skills in a practical and targeted manner, R‑Kon therefore offers individually tailored CAD training courses in which customers learn exactly what they need for their everyday work.
In terms of training content, there is a strong focus on the efficient creation of reusable models through predictive model composition as well as strategies for independent knowledge enhancement. Particularly interesting trainings for advanced users: The creation of scalable models with top-down design and sketch skeletons as well as the automation of models and processes in the CAD system using Inventor-iLogic and Inventor-API. You can find a taste of methods and content in the "CAD Tutorials" section and on the R‑Kon YouTube channel.
The training courses are designed to work very well as online events using contemporary tools. Face-to-face training sessions are possible, but not required. Public Inventor trainings with general content as well as face-to-face trainings are offered in cooperation with GFU Cyrus AG, remote and in-house trainings can also be booked directly at R‑Kon.
In all trainings, examples and topics are addressed and considered for setting focus as far as possible.
Appointments are arranged individually. Please use the contact options contact options to arrange a seminar date.
Automatisation of models and workflows, iLogic and the basics of API-programming in Inventor
In this iLogic seminar, participants will learn how to automatically control models and model parameters in Inventor using iLogic rules. One focus is on automating size increments and variant generation based on changes to input values.
In addition, the automatic provision of model-dependent data for tables, annotations, model properties (iProperties) or title blocks is practiced in the training. The transfer of dimensions, weights or areas from the model into tables and comments should generally not be done manually if possible due to the risk of errors when changing the model. Using iLogic to provide the values and parameters needed for automatically updating tables and annotations is another focus of this course.
This seminar gives the participants a basic understanding of iLogic and the Inventor API and enables them to independently find solutions with which they can automate models and workflows in their everyday work. It also familiarises the participants with the integrated tools such as the logger and the iLogic editor.
-
Conceptual basics of the automation of models and workflows in CAD
- What can iLogic automation be used for?
- When and why is this useful?
- How must a model be structured in order to be well automatable?
- If necessary, discussion of individual applications of the participants, which can be addressed by setting priorities or after completing the "standard agenda".
-
Exploration of the tools used, some simple examples
- Parameterliste und Variablentypen, Benutzerparameter und Modellparameter
- Activation conditions in features
- Equations in Variables
- iLogic rules editor
- Creation of simple assignments, queries and outputs
- Evaluation of expressions and Boolean logic
- iLogic logger
-
Automation of a simple part
- Weight or size dependent features
- Use of conditionals
- More extensive automation functions such as thread sizes or number
- Handling bad input values
- Integration of Excel spreadsheets
-
Automation of workflows, especially when entering or transferring data as text to be output
- External Rules
- Useful functions
- Loops
- Automatic modification of iProperties
- Opening input dialogs, error handling
- Automatic generation of parameters for the output of model or geometry properties on drawings
- Using enumerators
- Organization of external rules using forms
- Automatic execution of rules with iTrigger
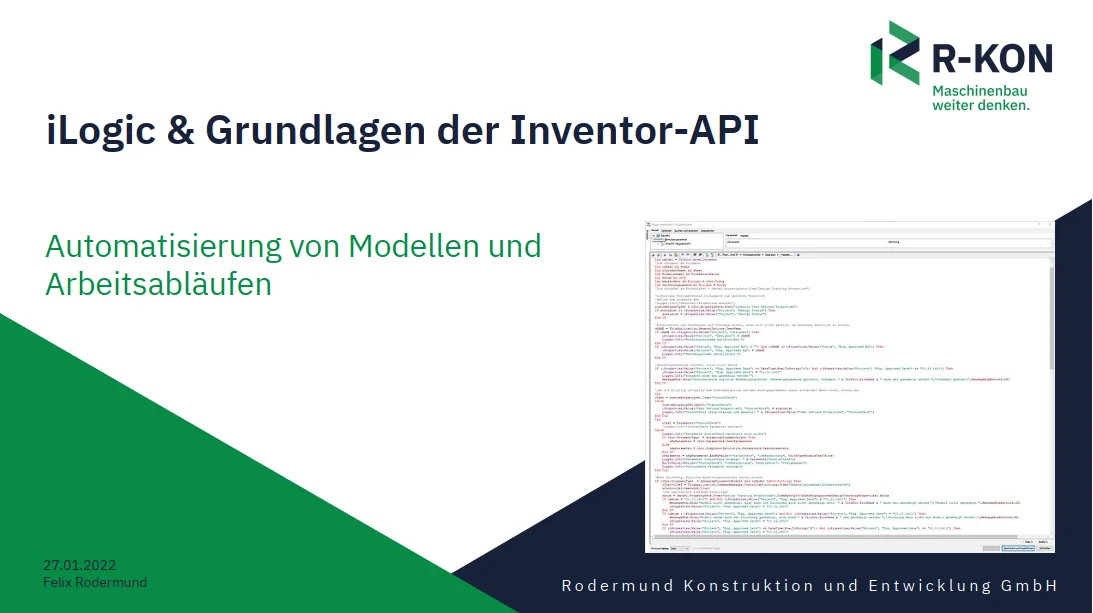
Strategically forward-thinking model creation
This seminar provides users who are already familiar with Inventor with more in-depth expertise and in-depth knowledge of different working principles and advanced methods. It lays the foundation for working as a key user and for defining CAD guidelines. The participants learn to set up models in such a way that foreseeable changes can be made with little effort and the required output documents and data can be generated efficiently. Particular attention is paid to the development of parametrically and coordinated scalable models and the efficient implementation of variants.
The basics of forward-thinking, structured model creation are explained. Before creating the first elements, the participants learn to plan a useful approach for building the model and to identify the relevant criteria and the most suitable method for building the model. A low-redundancy or redundancy-free model structure is of particular importance for most methods.
The stability of various model elements is examined and various best practices are shown, such as how sketches can be drawn in a geometrically stable manner and how elements can be given stable references. Various ways of transporting parameters and properties between models, especially derived parts and skeletons, are shown and practiced. The handling of multi-body parts and flexible assemblies as well as model states and their representations is also taught.
-
Planning before the first click: where do I come from and where do I want to go?
- Evolution of the model data from draft to detailed design
- Handling of input and output data, data interfaces
- Logical representation of the design constraints and the decision-making process
- Foreseeable changes and geometric variants, desired procedure for later adjustments
- mechanical interfaces and their cross-component synchronization
- "wrong" input variables in modified designs
- size grading
- Required output documents (drawings, volume models, videos, parts lists, ...)
-
Sensibly creating sketches
- Scope, interrelationships
- Avoiding redundancies
- Stable geometry and stable constraints
- Stable references in sketches
- Sketch hygiene
-
Structuring part models in a comprehensible and change-friendly way
- supporting geometry and subsequent geometry, mapping of the construction logic
- stable references in parts
- Bundling dependencies through work elements
- Pros and cons of various pattern types
- Welded or glued parts as multibody parts, derivation of the partial volumes for parts lists
- Derived parts (dissection, merging, finishing for subsequent process stages)
- Table-driven iFeatures and iParts
- Representation of several variants of a part
- Model hygiene
-
Creating assemblies that are realistic, stable, comprehensible in a result-oriented way
- BOM organization, ERP and PDM: What belongs in the assembly, how is the environment represented?
- Stable references and motion references in assemblies
- Pros and cons of generators
- Movable sub-assemblies, flexible installation
- Deformable components, adaptivity
- Depict and synchronise interfaces (skeleton, table, iLogic)
- Realistically depict movement states, position representations
- condition-based present components, assembly representations
- Assembly hygiene
-
Drawings
- Transfer model states into views
- creating stable references for views in drawing sketches or in the model
- Output parameters in parts lists or comments
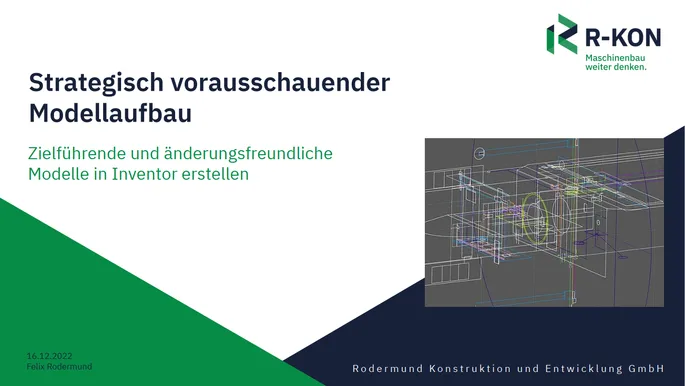
Inventor crash course
The Inventor crash course accompanies newcomers and newcomers to 3D CAD through the first steps. It guides you compactly through the most important work areas and explains how to use the most important functions for creating simple parts, assemblies and drawings. For this purpose, a simple example assembly from several parts as well as an assembly drawing and a single part drawing are created along the lines of a textbook.
After completing this crash course, the participants will have a rough overview of the functionality and operation of Inventor. You can create simple parts, assemble them into simple assemblies, and derive drawings from parts and assemblies. The participants can orientate themselves in the work areas used for this purpose. You can also identify the program environments and functions for which you need more in-depth knowledge and search for and acquire them in a targeted manner.
-
user interface
- General operation of Inventor
- Creating projects, files and editing their properties (iProperties, Options)
- Toolbar and tree view of the "Part", "Assembly", "Drawing" and "Presentation" workspaces
- Operating the model viewports and navigating in the model space
- Contextual radial menu and gesture control
- Using the tree view
-
part creation
- Creating and using sketches
- model origin; Create, use and edit work geometry
- Creation of simple bodies as extrusion and rotation
- Creating multi-body parts
-
sketch creation
- Sketcher environment tools
- Drawing basic elements (lines, circles, arcs, ...)
- Line types (geometry, auxiliary line/point, center line/point)
- Constraints, dimensions, degrees of freedom and stability
- Project existing geometry
-
Detailing of bodies
- details oriented tangentially or radially to round bodies, aligning work geometry to volume
- drillings
- creating patterns
- Cosmetics (chamfers, curves, external threads, ...)
-
assembly creation
- Methods for placing and creating parts in the assembly
- assembly relationships
- inserting of standard parts from the Inventor library ("Content Center")
- patterns of parts
-
drawing creation
- Base view, projected view, detail view
- sectional view, breakout
- Labeling and dimensioning on drawings
- Symbols
- BOMs and item numbers in assembly drawings
- Exploded view on drawing
- Position views
-
Miscellaneous
- Parameter list, user parameters, named dimensions
- Mathematical expressions in parameters
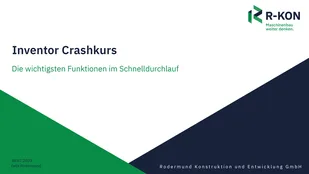
With all services offered, you benefit from R-Kon's high efficiency and excellent price-performance ratio.